New Product Launch: TaylorMade Project (a) and Project (s)
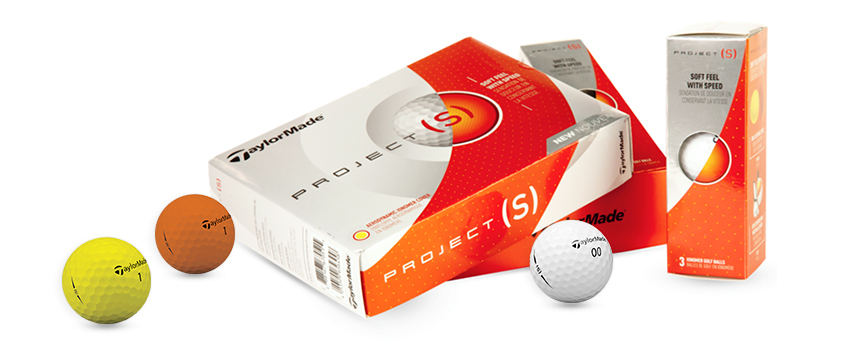
New TaylorMade Project (s) Golf Balls, image: todaysgolfer.com
The year was 2014. The research mavens at TaylorMade Golf studied golfers with handicaps between 10 and 27. They looked at approach shots from 150 yards and discovered that this caliber of golfer missed the green 17 out of 18 times from the white disk planted in the center of the fairway. And the average miss was by a whopping 35 yards.
TaylorMade’s conclusion? The company could engineer a golf ball to travel further, but golfers would not improve their scores unless they offered “Tour-like” performance on the many, many short shots that were needed around the greens. The result is the Project (a) that is designed to provide more spin and control off the mid-irons and hybrids that amateurs are employing on approach shots.
The Key is Multiple Layers
Of course, TaylorMade was not about to sacrifice the low-spin distance generated by its core golf balls off the tee. To achieve that driver distance and optimal launch condition, the engineering team adopted a multi-layer approach to golf ball construction. It required more than three dozen prototypes to come up with just the right proportion of mantle and core specifications under their proprietary Soft Tech cast urethane cover.
A mandate was to retain that urethane cover for TaylorMade golf balls. As Michael Fox, Category Director of Golf Balls & Accessories puts it matter-of-factly, “100% of worldwide Tours use a golf ball with a Urethane cover, while 0% use Surlyn. If every Tour player and Tour ball manufacturer in the world is telling you urethane is the best material, why wouldn’t you buy the only product outside the Tour ball category using this technology that’s now longer than ever before?”
Under that ultimate skin, TaylorMade has constructed a dual-core design for its Project (a) golf balls that is comprised of a larger and softer core that reacts with the stiffer outer core to add spin control on iron shots while not losing ball speed. The dynamic interplay between the action cores also helps pinch the club face against the cast urethane cover to generate additional greenside spin and precision.
What’s New for TaylorMade’s Three-Layer Design in 2018?
The TaylorMade Project (a) is dressed in the company’s 322 Dimple Seamless Cover that it employs on the Tour-caliber TP5 and TP5X golf balls that are favored by the likes of Dustin Johnson, Jason Day, and Sergio Garcia. The aerodynamic dimple pattern produces less drag for increased speed and distance. The Project (a) promises that same tour technology with accompanying soft feel.
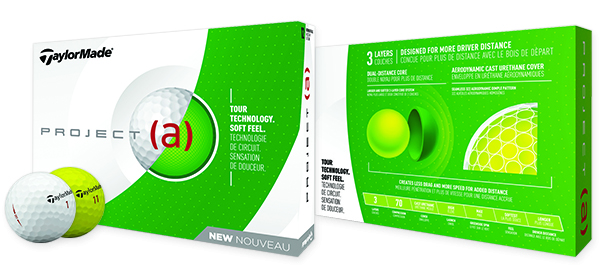
New 2018 TaylorMade Project (a) Golf Balls, image: taylormadegolf.com
In 2018, TaylorMade has also waded into the increasingly popular low-compression, soft-field space for slower swings with its new Project (s) golf ball. To bring the Project (s) down to a competitive price point, the urethane cover has been jettisoned and replaced with a stiffer ionomer cover that generates the speed necessary for longer ball flight on slower swings. Even without the urethane, TaylorMade has taken all pains to make the cover softer than comparable soft-feel balls.
Under the hood is a polymer mantle layer surrounding a 60-compression rubber core that is 10 points less than its cousin Project (a). That low compression typically causes golf balls to travel a shorter distance, but TaylorMade has fought the cut-back on distance-killing driver spin with a high lift 342LDP dimple pattern on the cover. With its emphasis on maximum distance and great feel off the clubface, TaylorMade looks to the Project (s) to eliminate the need for players with slower swing speeds from having to choose either distance or feel in a golf ball.
Both the Project (a) and the Project (s) are now available throughout the golf world. The Project (a) is offered in gloss white or yellow and the Project (s) can be purchased in gloss white or matte finishes of yellow or orange. All of these can be found at at Golfballs.com.